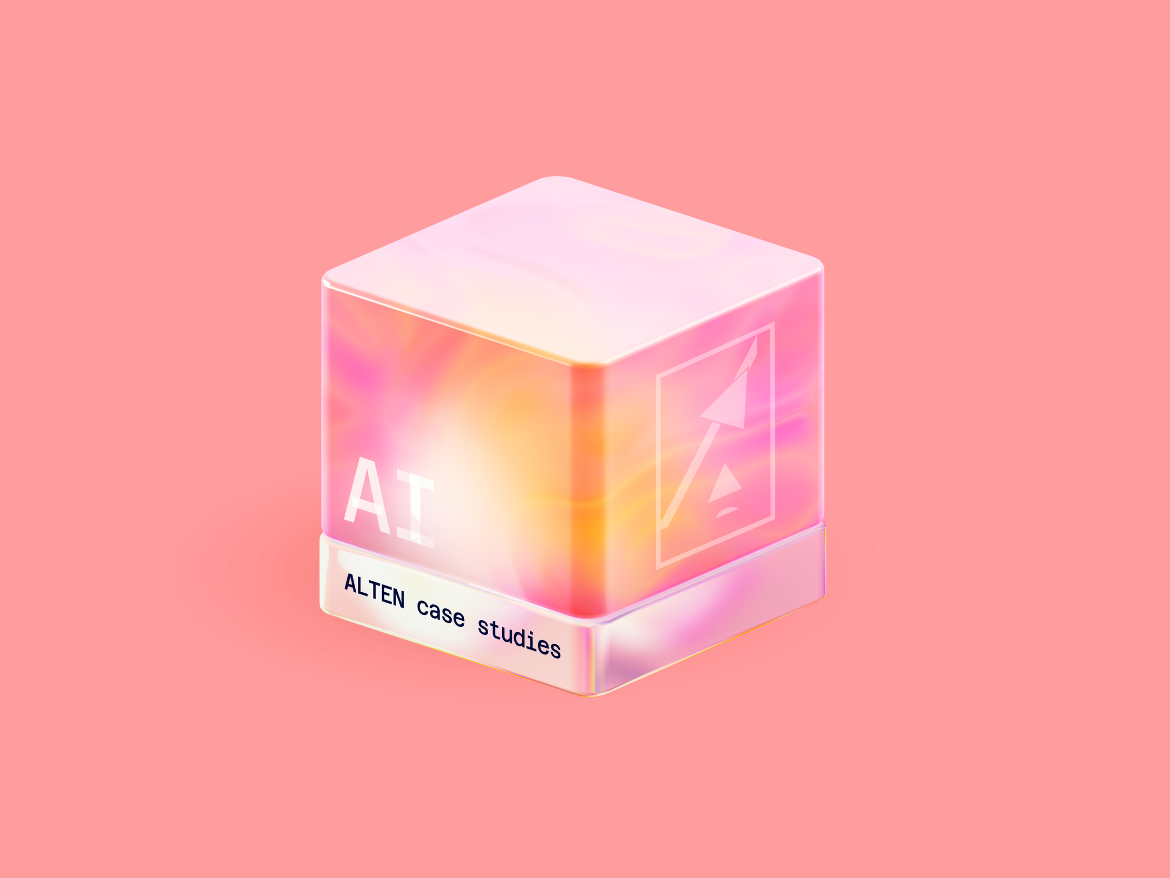
ALTEN is known for its expertise in advanced AI solutions for industrial optimization. ALTEN in Italia partnered with a high-volume manufacturer to address the challenges of maintaining consistent quality, reducing downtime, and enhancing sustainability. A cutting-edge, AI-driven solution transformed the client’s production processes, enhancing both operational efficiency and product quality.
ALTEN combined machine learning models and real-time monitoring to help a manufacturer of large-sized ball bearings shift from reactive to prescriptive quality level adjustments, while also reducing waste. Ball bearings are critical components in high-precision manufacturing; even minor inefficiencies can have a substantial negative impact on customers’ perceived value.
Challenge: Quality level prediction to improve efficiency while contributing to sustainability
Solution: An intelligent, quality level prediction algorithm with real-time dashboards
Benefits:
- Enhanced operational efficiency
- Heightened productivity
- Empowered operators
- Savings in infrastructure costs
- Reduction in negative environmental impact
Data-driven results
Identifying quality issues before the completion of the production process was particularly important to this manufacturer. ALTEN addressed this issue by applying the potential of AI, deploying a machine-learning model capable of predicting the quality of ball bearings up to an hour before the end of the production cycle. The model allows operators to make real-time adjustments, significantly reducing the rate of defective products and minimizing the amount of scrap generated during production. The benefits are felt both in cost savings and improved sustainability.
Actionable insights
The effectiveness of the AI system was further enhanced with the introduction of real-time dashboards to give operators continuous, up-to-the-minute insights into production parameters, machine health, and product quality. The dashboards offer clear, actionable data, enabling quick decision-making in response to any deviations in the production process, before they escalate into more significant problems. This empowers operators to maintain a streamlined, efficient workflow, improving productivity and quality control.
The results of ALTEN’s AI-driven solution were immediately apparent, including a 2% reduction in product scrap. Additionally, the transition to AI-powered predictive maintenance optimized the life of the machinery and lowered energy consumption, contributing to measurable sustainability benefits.
Futureproofing
Using cloud-based Microsoft Azure services, ALTEN ensured a scalable solution that allows the client to future-proof their operations and reduce the need for heavy on-site infrastructure investments. Clear cause-and-effect analysis makes it possible to pinpoint the root causes of quality deviations, enabling continuous refinement of processes and enhancing productivity. Azure Machine Learning, Data Factory, and other cloud services provide a seamless, low-cost platform for ongoing machine learning operations (MLOps), making the solution accessible and easy to maintain.
Revolutionize How You Maintain and Operate
Discover how AI is transforming maintenance from reactive to revolutionary—see what’s possible for your operation.